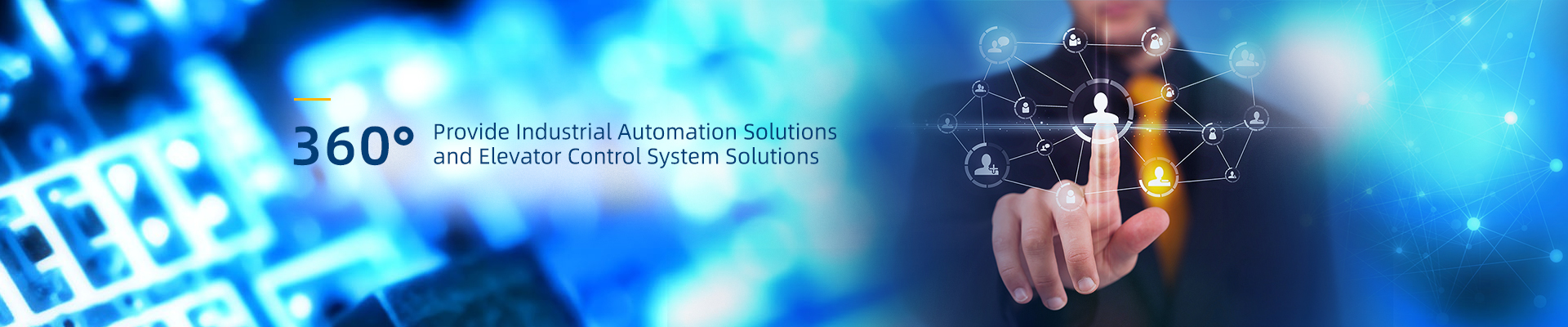
1 FOREWORD
Concave-printing Machine is a printing machine that performs overprint printing using a concave graphic pattern. The graphic portion of the printing plate is recessed, and the blank portion is on the same plane as the outer circumference of the plate cylinder.
When the Concave-printing machine prints, the full plate of the plate cylinder is inked, and the ink of the blank part of the plate is scraped off by the squeegee, leaving the ink of the graphic part, and then sent to the printing carrier (paper, plastic film, etc.). And then embossing on the back side of the printing carrier by the impression cylinder, the ink of the concave portion is directly transferred to the printing carrier, and then passing through the high temperature box to solidify the ink on the printing carrier, and stacking or rewinding the printing carrier through the winding process.
Concave-printing machines generally have printing functions of multiple colors and multiple patterns. There are several colors of color printing, it is necessary to have several colors of ink and plate rolls, and each version of the roll is synchronized by mechanical tradition to achieve color registration.
Modern printing is increasingly demanding on printing efficiency and printing quality, requiring printing machinery with sophisticated mechanical design and precise electrical control.
2 Transmission System of Concave-printing Machine
The main transmission system of the concave-printing machine can be divided into the unwinding part, the main motor driving part and the winding part. In order to avoid the influence of the eccentricity of the winding and unwinding substrate on the tension, it is generally added one after the unwinding stage and the winding front stage. The traction mechanism is the unwinding and winding traction.
According to the number of motors used in the whole system, the concave-printing machines commonly used in the industry can be divided into three-motor system, five-motor system and seven-motor system.
three-motor system
The three motors are the unwinding traction motor, the main drive motor, and the winding traction motor. The unwinding uses the magnetic powder clutch to control the tension, and the winding adopts the torque motor or the magnetic powder clutch, as shown in Figure 1.
five-motor system
The five motors are unwinding motor, unwinding traction motor, the main drive motor, winding traction motor, and winding motor, as shown in Figure 2.
seven-motor system
On the basis of the five-motor system, the automatic roll change function of the rewinding and unwinding part is added, that is, the winding is divided into the winding A-axis and the winding B-axis, and the unwinding is divided into the unwinding A-axis and the unwinding B-axis, as shown in Figure 3.
Tension system of concave-printing machine
Since the only difference between five-motor system and seven-motor system is the automatic roll change function, and this function can be completely guaranteed by the mechanical design and the logic control of the printer computer program under the condition that the electronic control system ensures constant tension control. Usually when debugging seven-motor system, we only need to debug the five-motor system successfully, and then setting the same parameter of winding A-axis B-axis and the unwinding A-axis B-axis, so that the seven-motor system can be operated. Therefore, for the sake of easy understanding, the five-motor system is taken as an example for illustration.
The concave- printing machine is generally distributed according to its tension control system. It can also be called a four-stage tension system. The four-stage tension is: the tension between the unwinding and the unwinding traction, the tension between the unwinding and the main motor, the tension between the main motor and the winding, and the tension between the winding traction and winding. During the printing process, the tension of the four sections should keep constant. In order to keep it constant, the main motor usually sets the operating frequency according to the production speed requirement. The unwinding motor, the unwinding traction motor, the winding traction motor, and the winding motor need to adjust the operating frequency of the respective motors in real time according to the operating frequency of the main engine and the actual tension of the materials of the respective parts, so as to achieve the purpose of constant tension.
3 Technical requirements
1) High speed accuracy
For concave-printing machine, many materials can withstand very little surface tension, and small fluctuations in tension may cause breaks. This material requires very little pulling force to produce, that is, it needs to maintain a small constant tension. So for the inverter, no matter what frequency control mode it use (PLC control frequency or use the built-in tension control function to calculate the frequency), the accuracy of speed control must be high to keep the tension constant.
2)Fast response to frequency command
Also in order to meet the constant tension control requirements, when the PLC controls the frequency, for the frequency command given by the PLC, whether the communication is given or the analog quantity is given, the inverter must respond quickly. And that is, the signal receiving and processing capability of the inverter should be strong, the accuracy should be high, and the inverter program should run faster.
3) Output torque stability
In some cases where there is no tension sensor, the tension control is completely dependent on the inverter's control of the output torque. At this time, the stability of the output torque directly determines whether the material tension is stable or not.
4) Wide range of speed regulation
For the concave-printing machine, it is necessary to run the debugging equipment at a low speed; it also requires high-speed operation to improve the production efficiency. At present, the speed of concave-printing machine used in the industry has been raised from the early 100m/min to more than 300m/min, which puts higher requirements on the speed regulation range of the inverter, not only requires low frequency torque characteristics, but also requires high speed control precision.
5) Accurate compensation for friction of mechanical equipment and fluctuation of acceleration and deceleration process
In actual production, due to the friction and inertia of mechanical equipment, as well as the speed fluctuations of the acceleration and deceleration process, it often affects the material tension. As a high-performance inverter with special functions for tension control, it is necessary to take into account the above effects and perform accurate compensation. It has reached constant tension control regardless of speed acceleration, speed reduction, start-up or stop.
Solutions
In view of the industry application characteristics of the current concave-printing machine, the HD50 high-performance vector control inverter developed by Shenzhen Hpmont Technology Co., Ltd. can provide a variety of solutions to meet the common needs and characteristics of different users and different printing equipment. The following are several solutions for achieving tension control by using HD50 high performance vector control inverters.
1) PLC+ inverter solution + tension sensor
In this scheme, the PLC performs the tension calculation, and the winding and unwinding inverter, the traction inverter, and the main engine inverter all adopt speed control. The PLC calculates the running frequency of the inverter through the tension calculation, and transmits the running frequency to the inverter through analog quantity or communication.
Advantages: Customers can develop and change PLC programs according to their own product features and changes.
2) Inverter + tension sensor
In this solution, the material tension is detected by the tension sensor and feed back to the inverter. The tension control and the coil diameter calculation are completely processed by the inverter.
Advantages: Since most of the concave-printing machines in the industry are equipped with tension sensors, this solution can save the cost of the PLC part without the need to make major changes to the existing mechanical structure.
3) Inverter torque control
In this solution, the tension sensor can be eliminated, and the motor torque detection is performed by the inverter to control the tension.
Advantages: the cost of the tension sensor and the PLC part can be saved, and the whole set of equipment failure points can be reduced, and it is convenient for maintenance.
As a high-performance vector control inverter, various solutions of the Hpmont HD50 inverter have been successfully applied to different customer sites. In addition, in the actual use process, Hpmont HD50 inverter has completely met customer requirements, and also customers have indicated that the use effect exceeds expectations. In product comparison, whether it compares the speed response, torque response or speed accuracy, Hpmont inverter can reach or even surpass foreign well-known brands.
4) Summary
HD50 is a high-performance vector control inverter with built-in tension control module. It has high speed precision, fast speed response, stable torque control, high reliability, low interference and strong anti-interference. It also improved a wealth of tension control features according to the process characteristics of the printing industry. Through the practical application verification in the printing industry, the HD50 series high-performance vector control inverter researched and developed by Shenzhen Hpmont Technology Co., Ltd. satisfies the high requirements of the driving control of printing equipment, and has won unanimous praise and recognition from customers.